Palletising and packaging robot
Robotised palletising and packaging lines
Palletisation and packaging is one of the most labour-intensive and cumbersome activities, which often leads to losses in some industries. This is why more and more companies are choosing to streamline this process by using robotics for palletising.
Industrial robots are very universal and work well both in the case of homogeneous products and elements of various shapes, dimensions, weight and materials. In each case, robots guarantee high efficiency , quality and increased production efficiency . Thanks to palletizing and packaging robots, it is possible to automatically sort , sort and arrange products in an optimal manner , which allows for the best use of the loading space.
Why bet on palletising and packaging robots?
The use of robots for palletizing and packaging brings many benefits, such as increasing work efficiency, reducing costs related to employing employees, greater precision and accuracy, reducing losses related to packaging damage and greater flexibility in production . Robotic palletization is the future that allows you to achieve success and increase company profits.
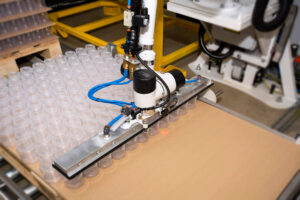
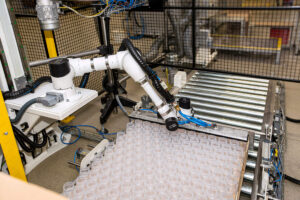
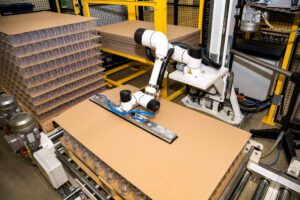
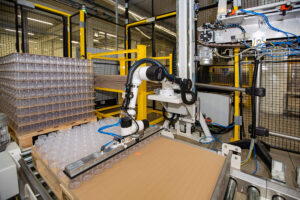
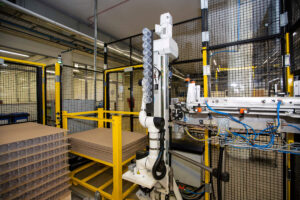
Do you need more information about our packaging and palletizing stations? Download folder!
Robotic palletisation - what does it involve?
Robotic palletization is the process of automatically placing goods into cartons or on pallets using industrial robots. Palletizing robots, as well as packing robots are programmed to move, orient and arrange products on pallets or other collective packaging according to a specific pattern and arrangement.
PREPARATION
Products enter the production line or convoy, in individual or bulk packaging.
PRODUCT IDENTIFICATION
The palletising robot can use a vision system or sensors to identify the position, orientation and dimensions of the products on the conveyor belt.
PRODUCT GRIP
The robot uses a suitable gripping tool (e.g. a jaw gripper, suction pads or other) depending on the type of products and packaging.
PRODUCT PLACEMENT
The manipulator arm moves over the target package and places the products according to a pre-programmed pattern.
CONTROL AND CORRECTION
If necessary, a vision system or sensors can check the correct layout of the products on the pallet. If inaccuracies or missing products are detected, the robot can make corrections.
What products can our robots palletise?
Our palletizing solutions are able to move and stack any package, regardless of its shape and weight. We design dedicated grippers for each application, so regardless of whether we are dealing with loose materials, liquid materials in containers, solid materials in cardboard boxes or other packaging, our palletizing lines and robots will ensure fast and precise operation.
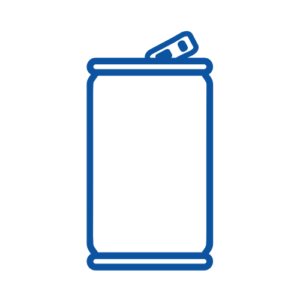
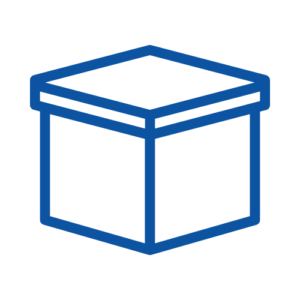
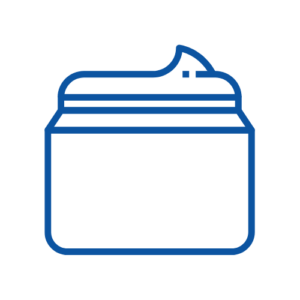
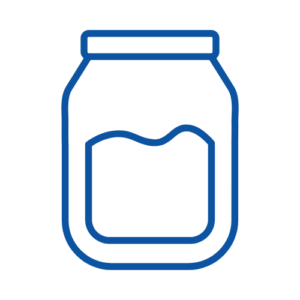
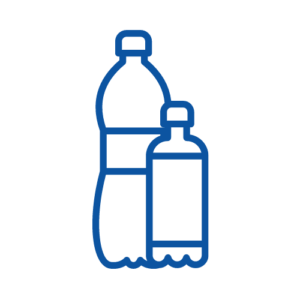
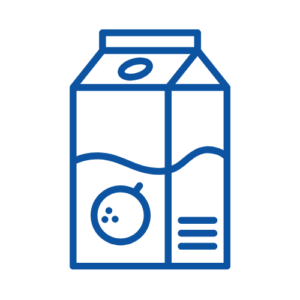
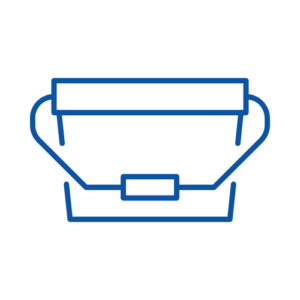
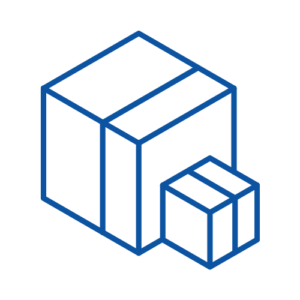
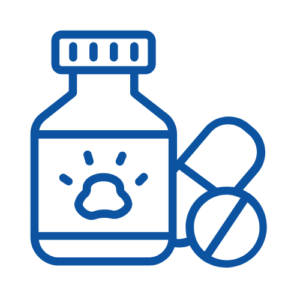
Where do Easy Robots robotic palletising systems perform best?
Our robotic palletising solutions are the ideal answer for industries such as:
Food industry |
Robots can palletize goods such as canned drinks,jars,milk cartons , bags with loose products, packages with frozen food, or boxes with fruit and vegetables. In the case of beverage bottles, cans or cartons, palletizing robots are able to arrange and stabilize various configurations, taking into account the variety of shapes and sizes of packages.
Cosmetic, chemical and pharmaceutical industry |
Palletizing robots can handle packages with cosmetics,liquids, cartons, bags, jars, as well as medicines and pharmaceutical products in various forms of packaging.
Production of packaging |
Robots can palletize various types of packaging, such as cartons, bags, foil bags, bottles and others.
Metal industry |
Industrial robots can palletize and pack workpieces, e.g. on press brakes and CNC machines.
What else our robotic palletising and packaging lines can help with:
- checking the weight or shape of the product and rejecting non-conforming items;
- detection of metals and other impurities in products;
- marking or labelling of products and packaging;
- checking the conformity and correctness of product labels;
- creating trays, displays and cartons, as well as packaging products in them;
- combining different types of products in bulk packaging;
- closing packages and checking that they are properly sealed;
- packaging of loose products while shaping them;
- applying corners, pads, dividers and lids to pallets of products;
- wrapping and labelling of pallets of products.
Explore a robotic palletising line for food products
The robotic packaging and palletizing station designed by us is intended for work with two foiling machines that allow packing and palletizing two different products at the same time.
In short, the task of a robotized palletizing line is to pack food products into collective cartons and then place the packages on collective pallets. With such a designed line and this type of products, each manipulator can pack up to 30 products in a box within a minute.
The post consists of several modules, each responsible for a different part of the process:
- carton folding module – cartons are delivered to the warehouse, from where the robot picks them up and folds them using a gripper with a servomotor. Then the carton is transferred to the feeder with a gluer and moved to the packaging area;
- packing module – Folding cartons are automatically positioned in the packing zone, where a mechanism keeps the top flaps of the cartons open, allowing products to be easily loaded. The manipulator alternately takes products from the foiling machines using conveyors and then places them in appropriate cartons. After the boxes are filled, they are moved to the closing and gluing area;
- closing and sealing module - on a conveyor with a gluer, the carton is closed and glued with the upper flap, and then transferred to the palletizing zone;
- palletizing module – cartons from both lines are alternately transferred to the picking zone, where the robot ES8 picks them up using a dedicated gripper and places them on a pallet. The robot also moves vertically to stack the cartons on the pallet to a height of approximately 1,900 mm. After the pallet is stacked, it is transported backwards by conveyor to the collection point. Full pallets can be picked up with a forklift or hand pallet truck;
- control module – the entire station is managed by the main control system, which integrates the control of all modules and sensors.
See our robotic Bottle Palletising Station
Robotic bottle packaging consists of several stages of work, each of which performs a different stage of the process:
1. bottle transport - the palletizing line has been adapted to work with the customer's device - an injection molding machine. Bottles are transferred from the previous device using modular transporters. The construction of the conveyor with an attached chain allows the bottles to be placed in a row. The method used keeps the bottles vertically, which allows them to be taken over by a pneumatic gripper;
2. bottle picking and stacking - Products transferred on the modular vacuum transport are grabbed by a pneumatic chuck that is attached to the ES5 robot arm. The suction method used in the handle allows you to pick up bottles from the transporter. Then, the ES5 manipulator, located on the 7th axis of the WIN-04 robot, places the bottles on a pallet placed on a roller belt;
3. stacking dividers on a pallet - when the layer of bottles is replenished, the robot feeds a new divider from the pallet divider positioning device and then arranges the next layer. This process is repeated until the pallet is filled with bottles;
4. full pallet pick-up - after the set number of bottle layers has been stacked, the filled pallet is moved to the pick-up location on a roller belt within the roller transport system. The condition for moving a pallet is the availability of space in the pallet collection area. If the sensor detects the presence of a pallet, the line is stopped until the previous pallet is received;
5. pallet replenishment - after collecting the filled pallet, an empty pallet is automatically taken from the transporter, provided that it has been previously replenished.
Manual palletisation versus robotic palletisation - when should I choose?
Choosing between manual palletizing and palletizing robotic depends on many factors that need to be considered to make the optimal decision for your company. The most important factors you should consider include:
Production volume and demand |
Investment costs |
Manual palletisation does not require a large initial investment, whereas robotisation can involve higher initial costs. If a company does not have the resources to invest in technology, manual palletisation is a good option - at least initially. As production increases, however, it is worth considering automating the process.
Labour costs |
Flexibility |
Workers are able to adapt quickly to changing needs, such as product variety or the need to work in other locations. It takes longer for a robot to changeover, which may make this packaging method seem less flexible, but modern robots are increasingly adaptable to changing conditions.
Efficiency and precision |
Ergonomics and working conditions |
Robotic palletisation reduces the risk of injury from heavy lifting and repetitive movements, and replaces humans for monotonous tasks.
info@easyrobots.eu
+48 608 697 888
What do you gain by investing in palletising and packaging robots?
The biggest advantages of palletizing and packaging robots Easy Robots are:
Flexibility - Robotised packaging and palletising covers any product range, is suitable for working in different conditions and for both short and long runs. Various patterns of product placement on the pallet are possible, as well as cooperation with other stations in the production process, the possibility of operating several lines at the same time and performing various operations throughout the palletising cycle.
Efficiency and economy - The palletising robot operates continuously 24 hours a day, 7 days a week. It is reliable, as it requires no downtime, except for maintenance downtime. It is characterised by its high working speed and its ability to perform several operations simultaneously.
Precision – industrial robots provide a high degree of repeatability of the tasks they are trained to perform.
Reliability - the components used in the robots have a long service life, which guarantees uninterrupted operation and reduced maintenance. In addition, the software provided enables the robots to be diagnosed and monitored in real time to counteract potential problems.
Intuitive operation - The robots have a friendly and simple interface, the operation of which we teach during our implementations.
MAKE AN APPOINTMENT FOR A FREE CONSULTATION!
WE WILL ADVISE YOU!